Iron and Steel Foundries
Lungmuß Feuerfest is one of the leading suppliers of refractory products for iron and steel foundries.
Coreless induction furnaces
The portfolio for coreless induction furnaces comprises neutral, acid and basic dry ramming mixes and patch and repair compounds.
And all materials for:
- Furnace spout, tapping spout
- Kiln hood
- Top ring
- Coil grout
- Insulation (mica products)
- Furnace floor
- Push-out block
- Covers
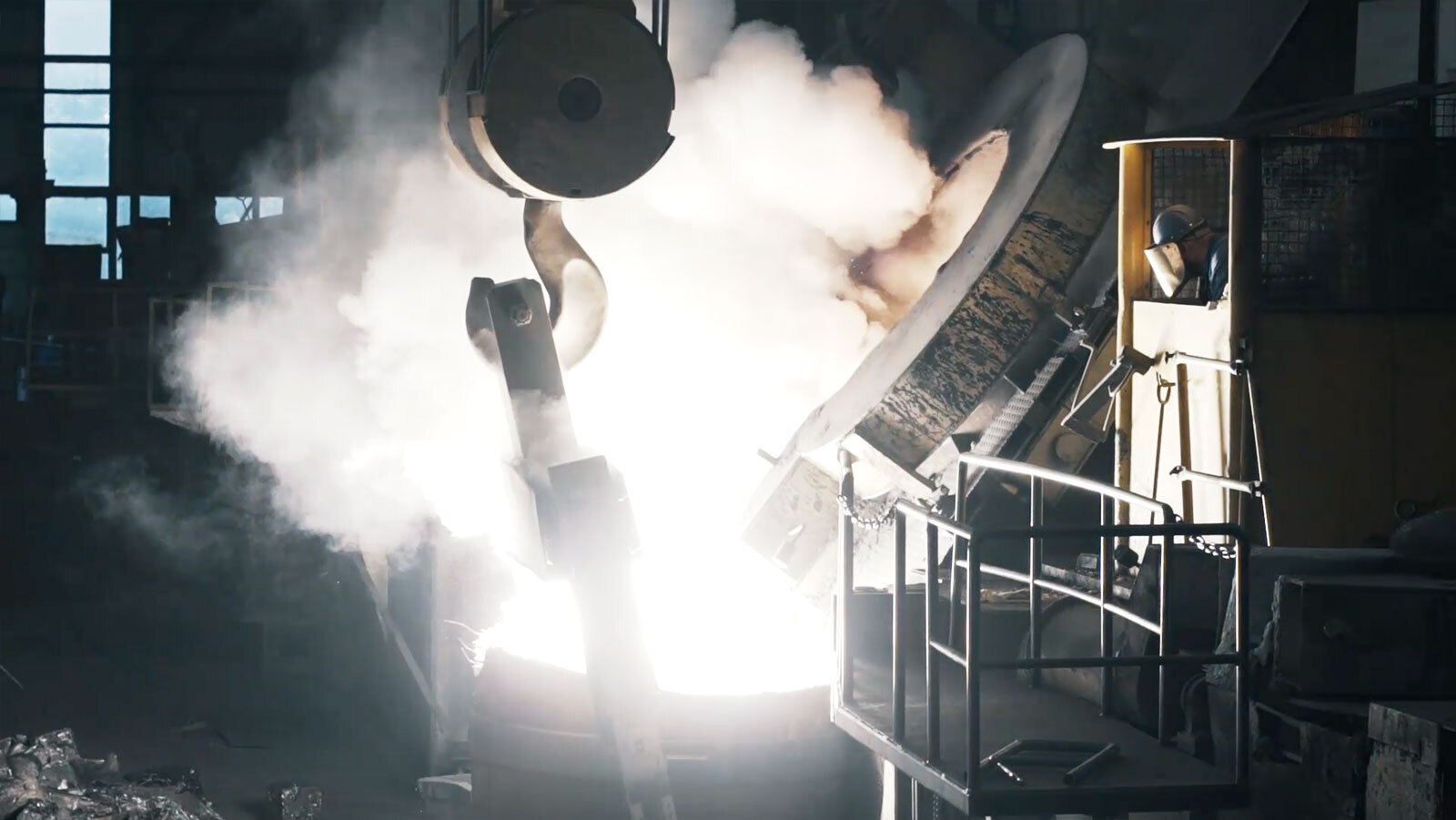
Cupola furnaces
For cupola furnaces, Lungmuß Feuerfest offers castables, ramming and gunning compounds for the lining of all relevant areas:
- Siphon
- Special fast-drying qualities for short shutdowns
- Taphole and hearth
- Melting zone
- Stack
- Charging zone
- Exhaust gas line and combustion chamber
- Dust separation
- Runners
- Forehearth
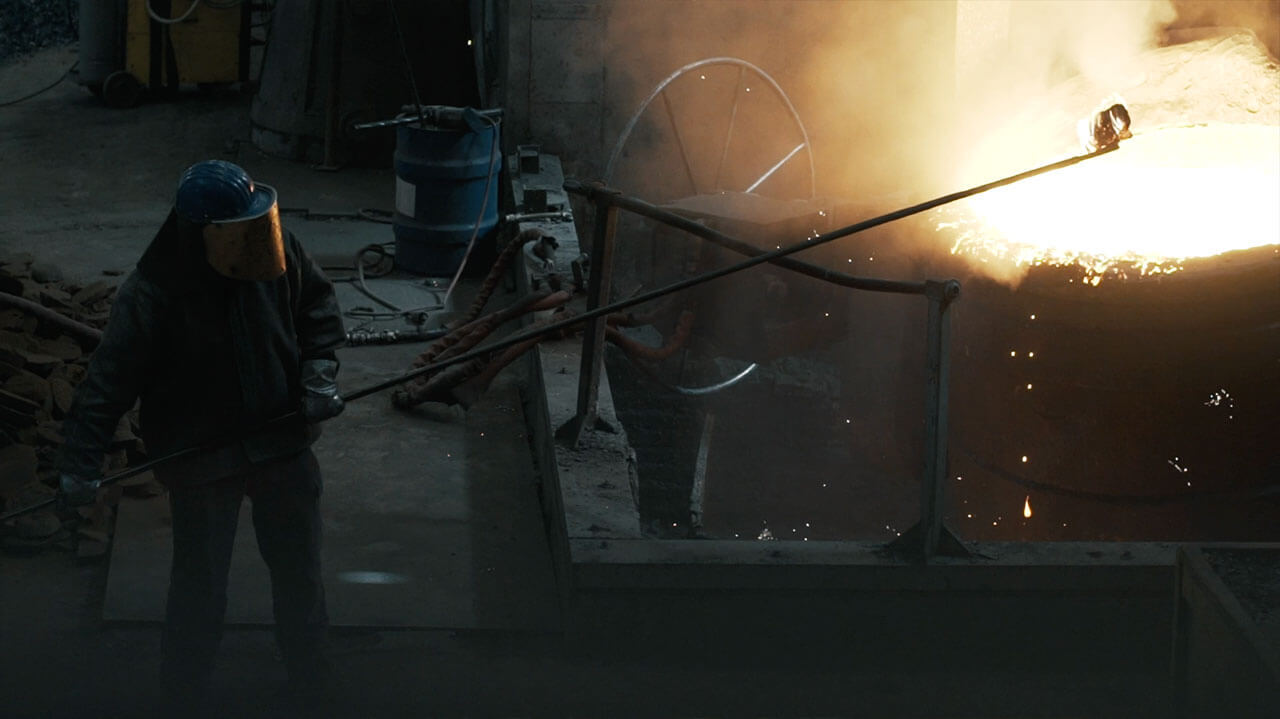
Ladles
The portfolio of refractory materials for ladles contains:
- Transportation vessels
- Treatment vessels and converters
- Mg-treatment for spheroidal graphite iron
- Casting vessels
- Mezger ladles
- Crane casting ladles
- Unheated casting machine
In addition, Lungmuß Feuerfest offers:
- Insulation and lining concepts for optimised energy balance and casting quality
- Complete lining and drying monitoring on-site by deploying its own service technicians
- Complete lining and drying service of foundry ladles and vessels in the department of prefabricated parts
Lungmuß Feuerfest offers the complete service for casting and holding furnaces: In addition, complete lining and drying of furnace vessels, in particular casting furnaces and forehearths as changeable replacement aggregates can be installed quickly. This leads to an increase of the plant availability and to a reduction of shutdown times.
Prefabricated parts
In the production department for prefabricated parts, Lungmuß Feuerfest develops tailor-made components, such as:
- Runners
- Runner segments
- Spouts
- Ladle weirs
- Converter plates
- Impact pads and ladle bottoms
- Well blocks
- Gating systems
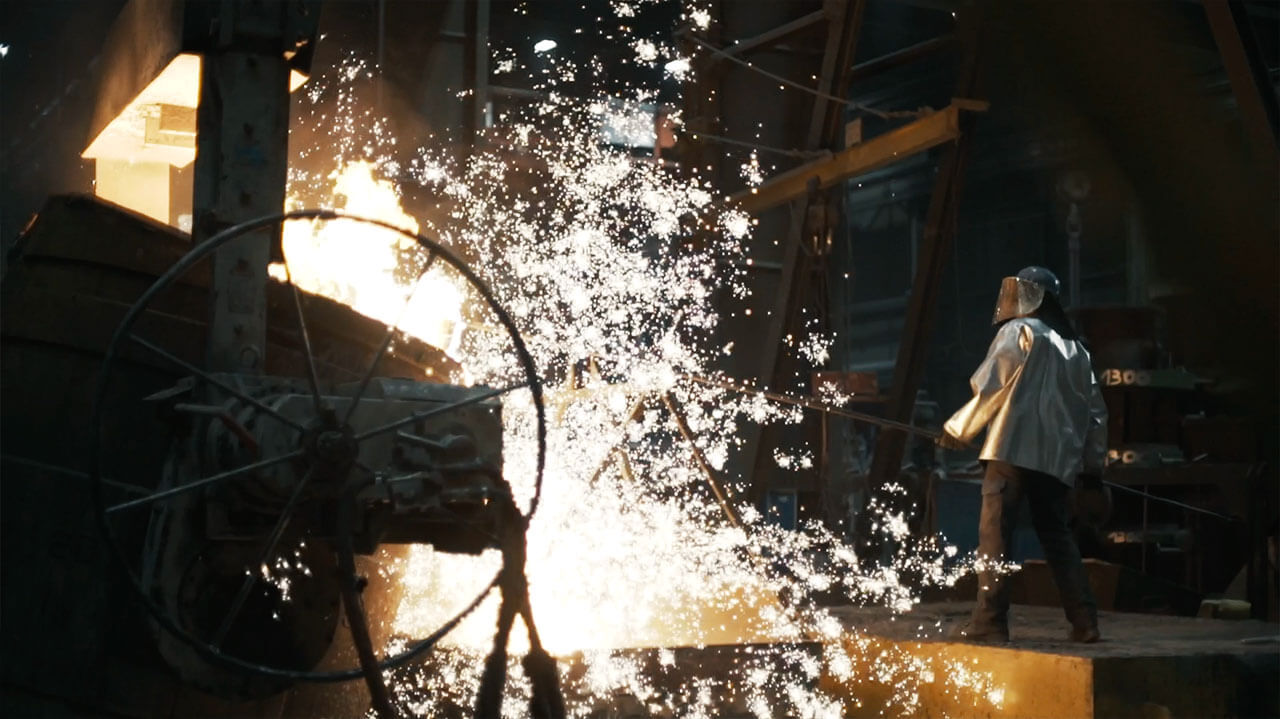
Full-service for foundries
Lungmuß Feuerfest offers optimal lining solutions, as well as homogeneous, complete drying of equipment used for transportation, handling, holding and casting:
- Ladles of all types
- GF converters
- Forehearths
- Casting furnaces
The services can be tailored to the customer requests and encompass:
- Engineering: heat transfer calculation, insulation concept, the selection of suitable insulating and refractory materials
- Breakout and disposal of worn-out refractory material
- UVV-check
- Installation of insulation and refractory material
- Optimal drying: Supply of ready-for-use vessels (no released steam during commissioning)
The benefits for the customer include the significant reduction of downtimes due to: Lining and drying times are eliminated, as are refractory installation works that interfere with the production. In addition, the service life as well as the plant availability and efficiency are increased.
Occupational safety risks, which emerge from the assignment of contractors at the customer facility, can be reduced just as contamination resulting from refractory installation.
Particularly noteworthy are the savings regarding energy costs incurred for drying and the administration costs incurred for handling and storage.